Plastic extrusion, such as UPVC (rigid polyvinyl chloride) profiles or pipe products, is mainly formed through the mixing, extrusion processing, shaping, haul off, and cutting of PVC resin and related additives. The factors that affect the performance of products cover every step in the production process. Each step interacts and affects each other through the media of the product. One problem can be compensated for by other steps within a certain range, so each step becomes an organism. Among them, raw materials, formula equipment and operating techniques are the main factors in plastic extrusion process, which directly affect the quality and output of extrusion molding. This article focuses on the impact on extrusion from the perspective of extrusion equipment and raw materials.
Generally, PVCproducts use the following additives to do extrusion process:
1.PVC resin:
Polyvinyl chloride, referred to as PVC in English, is the third most produced synthetic polymer plastic in the world (after polyethylene and polypropylene). PVC was once the most widely produced general-purpose plastic in the world and was widely used. There are two types of PVC: rigid (sometimes abbreviated as RPVC) and soft. Rigid polyvinyl chloride is used in construction pipes, doors and windows. It is also used to make plastic bottles, packaging, bank or membership cards. Adding plasticizers makes PVC softer and more elastic. It can be used in pipes, cable insulation, flooring, signage, phonograph records, inflatable products and rubber substitutes.
stabilizer:
Because PVC resin is a heat-sensitive resin, it begins to thermally degrade when the temperature reaches about 90 to 130°C, releasing unstable HCL and causing the resin to turn yellow color. As the temperature rises, the color of the resin becomes darker and the physical & chemical properties of the product decrease. In addition to improving the production process of resin raw materials, solving the degradation problem mainly involves adding stabilizers to PVC resin to absorb and neutralize HCL gas and eliminate its catalytic degradation effect. Commonly used stabilizing systems include: lead salts, organotin, metal soaps and rare earth stabilizers.
Lubricant(PE wax or Paraffin):
One kind of additive to improve lubricity and reducing interface adhesion. According to functions, they are divided into external lubricants, internal lubricants and internal & external lubricants. The external lubricant can reduce the friction between the material and the metal surface to prevent the UPVC material from adhering to the barrel and screw after plasticization. The internal lubricant can reduce the friction between the particles inside the material, weaken the cohesion between molecules and reduce the melt viscosity. The use of lubricants has a significant impact on reducing screw load, reducing shear heat, and increasing extrusion output. The design of the lubricant in the formulation is very important.
Filling material:
In order to improve the hardness and rigidity of products, reduce product deformation, and reduce raw material costs, fillers such as CaCO 3 are often added to the production of UPVC products.
Processing Modifier (ACR):
The main purpose is to improve the processing performance of materials, accelerate the plasticization of PVC resin, and improve the fluidity, thermal deformation and surface gloss of products.
Impact modifier:
The main purpose is to improve the impact resistance of products, improve the toughness of products, and improve the plasticizing effect. Commonly used modifiers for UPVC are CPE (chlorinated polyethylene) and acrylate impact modification.
The plasticizing mechanism of plastic extrusion equipment and the influence of formula ingredients on it:
There are many equipment for plastic extrusion molding. The main ones used for extruding UPVC hard products are counter-rotating twin-screw extruders conical twin screw extruder. The following mainly discusses the plasticization mechanism of commonly used extruders for extruding UPVC products.
Counter-rotating conical twin-screw extruder:
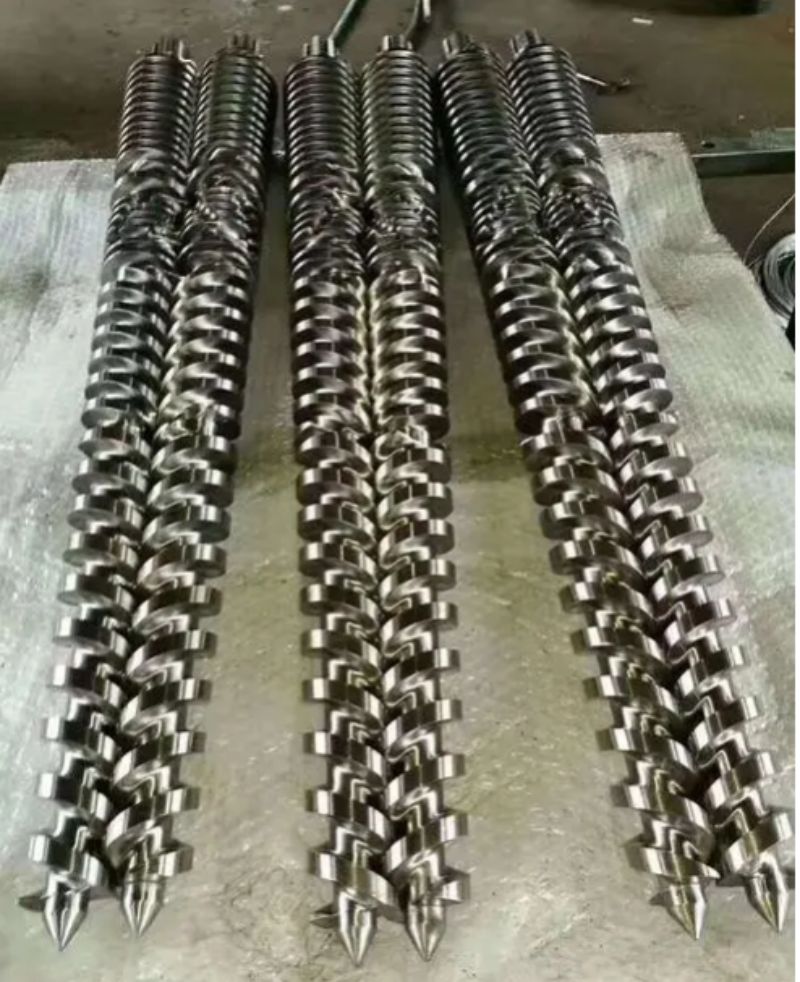
Post time: Dec-29-2023